The torque rheometer, also referred to as a laboratory kneader, plastograph, plasticorder, or “Brabender”, holds significant importance as a testing instrument within the PVC industry. Its role extends across both the quality control of raw materials and finished products, as well as in the realm of product development, particularly focusing on rigid PVC. Essentially functioning as an “extruder” with notably short screws, it features an enclosed chamber conducive to conducting measurements at varying temperatures.
It deceives to appear as a seemingly simple measuring method, and it starts with the fact that this method is not absolute, like a titration in analytical chemistry. Let’s take a closer look at this:
1. Understanding to Use the Torque rheometer:
The outcomes of these measurements are intricately influenced by factors such as temperature, rotational speed of the kneader, and filling volume (not to be confused with filling weight). This equipment efficiently applies considerable friction (torque) to the dry blend within a concise timeframe. Typically, the results of a kneader experiment are represented through a torque vs. time graph, as illustrated in Figure 1.
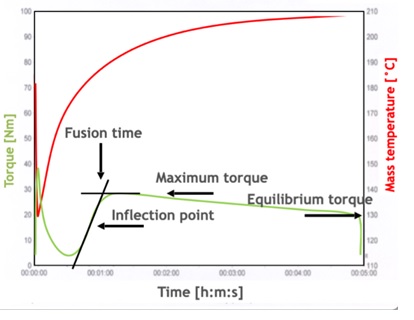
Figure 1 A typical graph of melt temperature and torque vs. time
[Copy rights: M. Schiller]
2. Challenges – Dryblend:
Before any measurement make sure that the dryblend had time to relax at least over night and better for 24 hrs. Otherwise the reproducibility will go down. If you have a series of many trials:
- Use Trial 1 always as a reference and repeat it after each 5 – 10 trials.
- Measure the series on the same day without any unnecessary break.
3. Challenges – Test Conditions:
- It is recommended by Brabender company that the start temperature and the end temperature shall not have a difference more than 20 degree. Otherwise reproducibility might drop.
- You have to think in volume (mL) NOT in mass (g)! For dryblends having a similar bulk density you can work with gram. Different bulk density might be the consequence of different filler contents.
- Don‘t start the measurement when „Mixer temp.“ and „Start temp.“ have a difference of more than 2 degree! – What will happen in the other case? Lower temperature means:
- Fusion will be delayed.
- Melt temperature will be reduced.
- Melt viscosity will increased.
- Maximum torque will be increased.Vice versa for higher temperatures…It will be difficult to compare results in one series! (Figure 2)
- Don’t change the speed of the kneaders in a series! – What will happen in the other case? Lower rpms means:
- Fusion will be delayed.
- Melt temperature will be reduced.
- Melt viscosity will increased.
- Maximum torque will be increased. Vice versa for higher rpm.
- The filling level of the mixer chamber shall be about 70%. Keep it constant. – What will happen in the other case? Lower sample mass means:
- Fusion will be delayed.
- Melt temperature will be reduced.
- Melt viscosity will increased.
Maximum torque will be increased. Vice versa for higher sample masses.
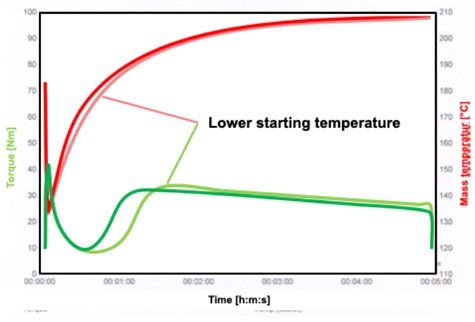
Figure 2 Shift in the typical graph of melt temperature and torque vs. time when the experiment was started at lower temperature
[Copy rights: M. Schiller]
4. Acceptable Tolerances:
- Fusion time (experimental error: +/- 15%)
- Maximum torque (experimental error: +/- 2%)
- Equilibrium torque (experimental error: +/- 2%)
6. Keywords:
PVC #stabiliser #stabilizer
PVC manufacturers, stabiliser producers, researchers, and regulatory bodies collaborated closely to devise and implement sustainable solutions. Technological breakthroughs, such as pioneering stabiliser formulations and process optimisation techniques, played a pivotal role in surmounting the challenges entailed in eliminating lead from PVC formulations.
As the global sustainability movement gains traction, the demand for lead-free PVC stabilisers is projected to escalate. Platinum Industries, as a member of the Indian Vinyl Council (IVC), has been progressively investing in research and development to yield high-quality and sustainable PVC stabilisers, thereby setting a precedent for the industry. Platinum Industries Ltd., the prominent PVC stabiliser manufacturer in India, also stands as a member of the Indian Vinyl Council (IVC).
Platinum Industries Ltd., a member of Indian Vinyl Council (IVC)